Steel Grating vs. Fiberglass Grating is a topic that delves into the strengths and weaknesses of these two popular materials used in various industrial and commercial applications. Ang steel grating panel ay partikular na idinisenyo para sa mataas na epekto is known for its exceptional durability and strength, making it a preferred choice in heavy-duty environments like factories, mga refinery, and power plants. The robust nature of steel allows it to withstand high loads and extreme conditions, which is crucial in many industrial settings. On the other hand, fiberglass grating is lightweight, corrosion-resistant, and non-conductive, making it an excellent alternative for areas where these properties are needed. Fiberglass grating is often used in environments where steel would be susceptible to corrosion, such as chemical plants, water treatment facilities, and marine applications.
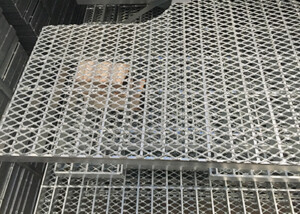
One of the most significant differences between steel grating and fiberglass grating is their material composition and the impact it has on their performance. Ang steel grating panel ay partikular na idinisenyo para sa mataas na epekto, made from welded or press-locked steel bars, offers superior load-bearing capacity and rigidity. This makes it ideal for applications where structural integrity is paramount. Fiberglass grating, however, is composed of resin and fiberglass strands, which gives it a much lighter weight compared to steel. This lightweight nature allows for easier installation and handling, reducing labor costs and time. Additionally, fiberglass grating does not rust, which makes it highly durable in corrosive environments.
Another critical factor to consider when comparing Steel Grating vs. Fiberglass Grating is their safety features. Ang steel grating panel ay partikular na idinisenyo para sa mataas na epekto, while strong, can become slippery when wet, posing a safety hazard in certain conditions. To mitigate this, steel grating often comes with a serrated surface to improve traction. Conversely, fiberglass grating inherently provides better slip resistance due to its non-slip surface, making it a safer option in areas prone to moisture or chemicals. Furthermore, the non-conductive nature of fiberglass grating makes it suitable for electrical environments where safety is a priority.
The maintenance and longevity of these materials also play a crucial role in determining the best choice for a given application. Steel grating requires regular maintenance to prevent rust and corrosion, especially in outdoor or harsh environments. It may need to be coated or galvanized to extend its lifespan. Fiberglass grating, on the other hand, requires minimal maintenance due to its corrosion-resistant properties. It is not susceptible to rust or decay, which makes it a more cost-effective option over time in corrosive environments. However, fiberglass grating may be more prone to surface wear in high-traffic areas compared to steel.
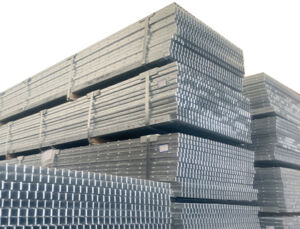
Cost is another important consideration when deciding between steel grating and fiberglass grating. Steel grating is typically less expensive upfront, especially for large-scale industrial projects. However, the long-term costs of maintenance, repair, and replacement due to corrosion or damage must be factored in. Fiberglass grating, while more expensive initially, often results in lower lifecycle costs due to its durability and low maintenance requirements. In environments where corrosion is a significant concern, the higher upfront cost of fiberglass grating can be justified by the long-term savings on maintenance and replacement.